Season’s end: preparing Halley VI for the winter
20 February, 2023 Halley
Martin Bell, Halley Vehicles Engineering Manager, reflects on the work of the Vehicles team as the Halley Research Station closes for winter.
This award-winning and innovative research station provides scientists with state-of-the-art laboratories and living accommodation, enabling them to study pressing global problems from climate change and sea-level rise to space weather and the ozone hole – first discovered at Halley in 1985. Halley VI is also the world’s first re-locatable research facility, designed to have longevity in its placement on the Brunt Ice Shelf. Although the station isn’t staffed during the winter, automation of instruments and experiments means that science takes place there throughout the year.
Engineers and support staff like Martin play a crucial role making it possible for scientific work to take place in this extreme environment.
As Vehicles Engineering Manager, I’m happy to say that vehicles are essential to the operation at the Halley VI Research Station. They need to work around the clock and at all temperatures to keep the station safe and operational. Throughout the season, it’s our job to keep the station running, and to maintain this special place for the winter and future seasons.
The vehicle garage at Halley VI is quite a special place for me. It was one of my first projects I helped to build in 1992! It was fabricated by a company called VM fabrications and shipped to Antarctica in kit form. Over its life the building has cost very little and has been the home for many mechanics. It’s warm and well equipped. We don’t have the luxury of running to the shops or parts deliveries – so it’s well equipped well and if we don’t have a part we can normally repair or come up with a solution to get by.
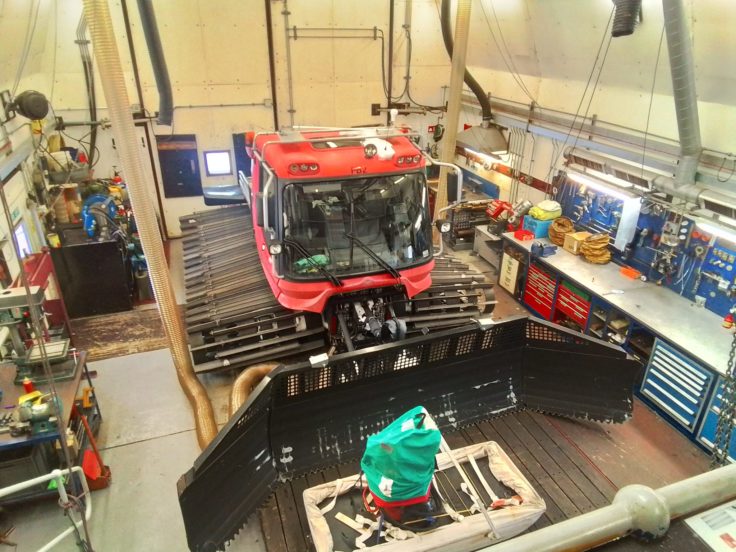
We have two CAT D6 LGP high drive bulldozers – incredible machines and invaluable to our operations here. Basically it’s a shovel on steroids. For those who read this blog who have been here in the old days the vehicle fleet has come on a long way since Muskegs and IH dozers! The Cat is fitted with a large winch and these are used to relocate the Garage and Drewry buildings once a year.
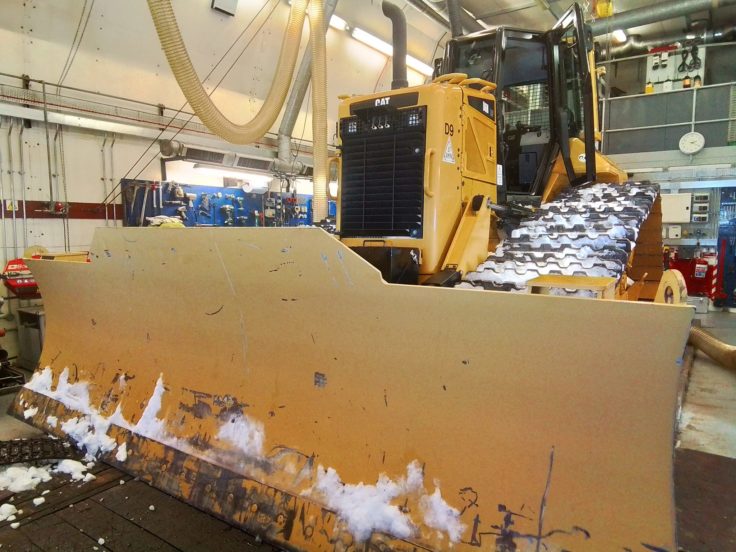
Nothing is straightforward in Antarctica. The CAT is a large mass of steel, so we have to warm and cool the machines slowly because all the steel expands and contracts at different rates. Seals can leak until all the steel has either warmed or cooled to the ambient temperature; we also get a lot of melt water off the vehicles so we collect the water and filter through a separator so no oil goes outside the building. Then to get the vehicles in we can open the front of the building via hydraulic doors, exposing everything to windspeeds of 20 knots. We have to be quick as the kettle can freeze if the doors stay open too long !
Some of the residents of our garages are more unusual – such as these Nansen sledges that are used for science work off station. We service and clean these before winter in preparation for use next year. Why do you still use wood, you may ask, and not some modern material? Well simply, it flexes and can be fixed easily. In this modern age, sometimes the simplest things are still the best.
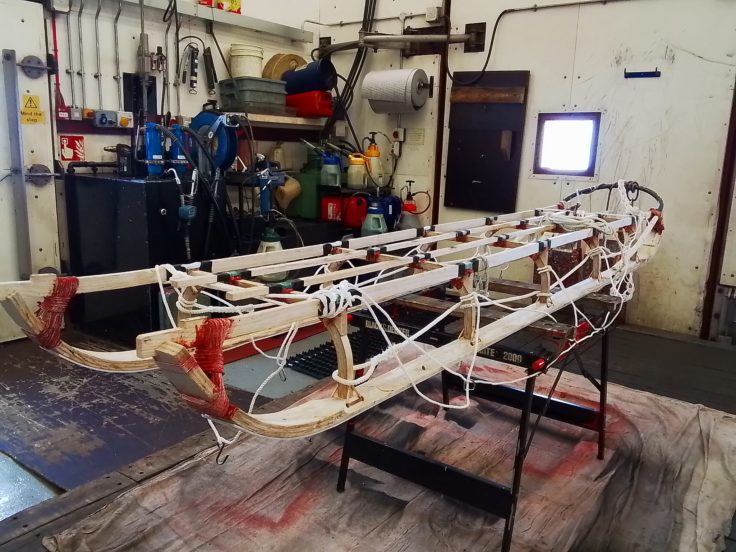
You would think water production would be easy on a continent covered in ice and snow, but it’s actually quite hard and can be expensive. Old Halley stations had restrictions on how much water we could use and all of the snow had to be shovelled by hand. Halley VI is different though: at the design stage the aim was to make water much more cheaply and efficiently, so the current systems all use waste engine heat and a large melt tank that can be filled by a dozer. The system is computer controlled and we can move water around the tanks to utilize reclaimed heat from the generators. Even better, the whole station runs on 40kw of power.
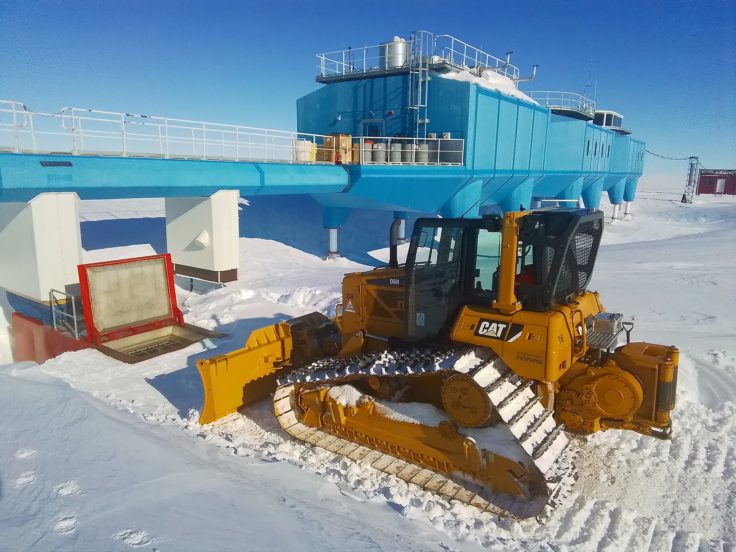
The whole research station is perched on adjustable ski legs, so that the station can be relocated. Raising the legs of the station is a necessary part of maintaining the station in preparation for snow through the winter season. Before we can do this we have to reset all 36 legs so that they are resting on top of the snow. The process is quite simple – first we have to gain access to the legs, which involves removing lots of snow and making safe access for the vehicles. We then place a support tower under the building and raise one leg at a time and push snow under.
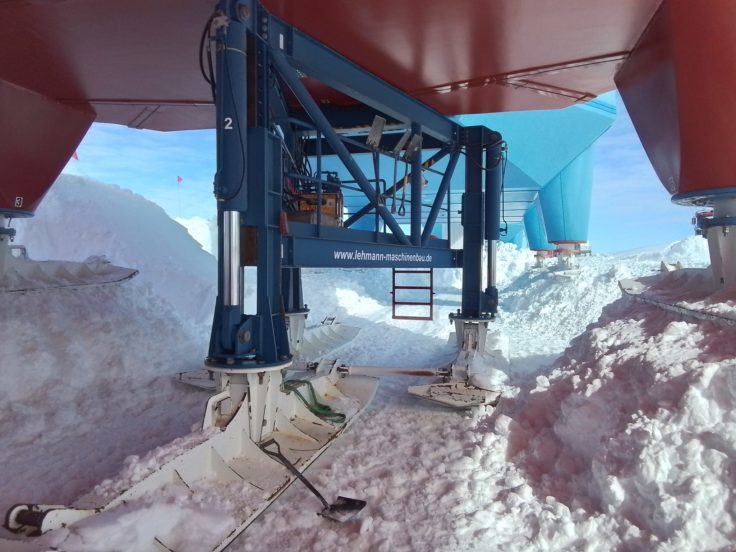
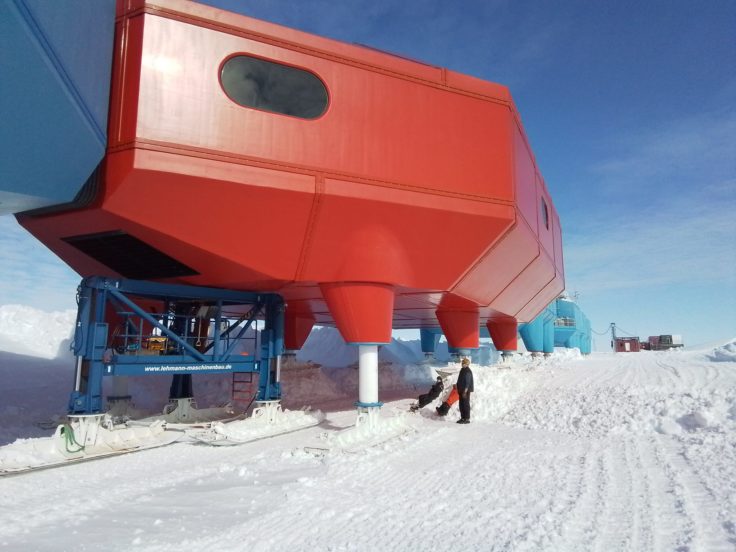
We then lower the leg down onto the mound and take the weight back onto the leg. This isn’t a small job – it takes three days to reset all the legs. Once all this is done we can raise the whole building, infill… and the repeat the process, to raise the station around 2m in total.
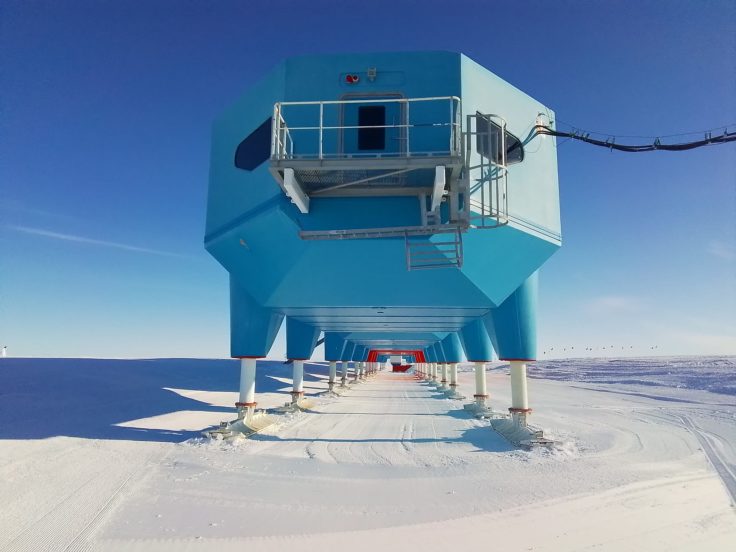
As the summer season came to a end, the station was looking good for the winter and lots of science has been done. In those final days, a big section of the ice shelf calved. The Halley IV, V and VI old sites have now gone for a cruise out into the Weddell Sea – meanwhile, the current station is safe due to years of preparation, and it’s a credit to the design of this station that we can move it!
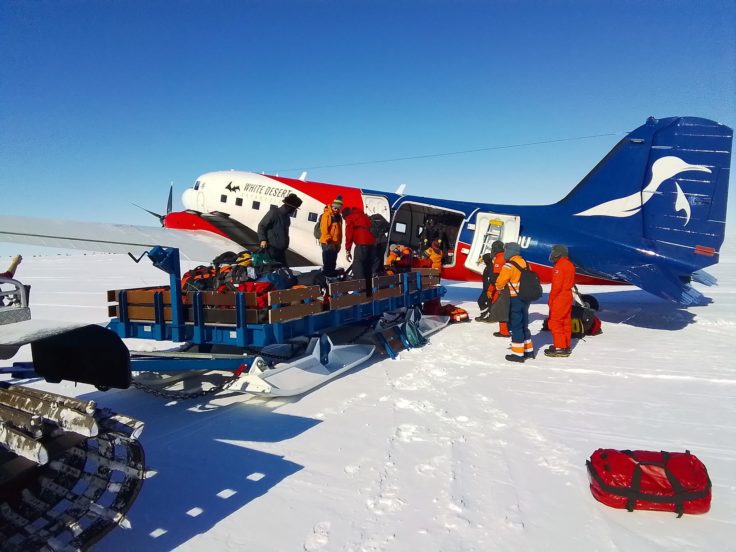
Most of the Halley team departed at the end of January 2023, leaving a of five of us for around two weeks to stay to batten down the hatches and prepare the station for winter. We used this time to slowly drain down systems and park the last of the vehicles up. One of the systems that gets turned off is the water – which means a more basic final few days with no more showers! As part of our work, we moved out of the main station and back into the auxiliary building for the last few days.
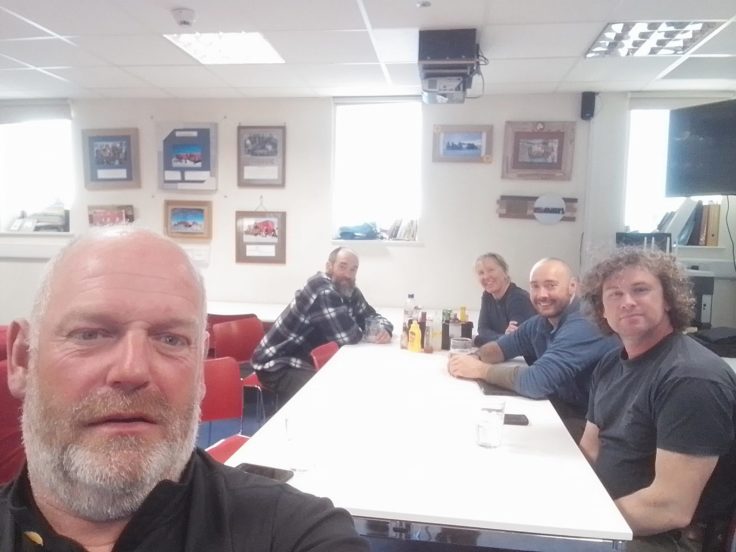
As the sun set on this season’s adventure, temperatures were falling to around -22’C. Those final days are always a time to reflect on things and everyone was in high spirits. It’s been a great season, and after being away from BAS for a few years it’s been wonderful to see the Station again and catch up with old friends again. People just keep coming back!
Even though we have now left the station unstaffed for the winter, amazingly the science continues. We leave a little turbine engine running and this keeps the science equipment running and data feeds back to Cambridge, part of the automation project that we’ve brought into action over a few years.
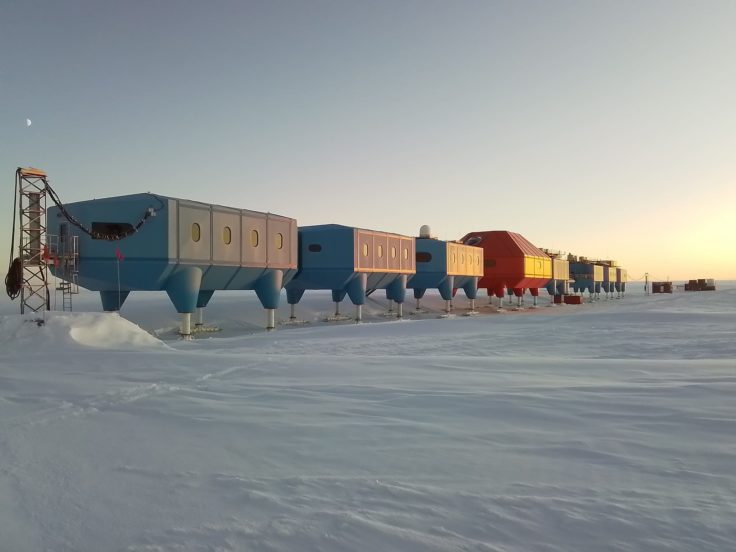