Behind the big blue door: the workshop helping to drive Antarctic science
28 March, 2025 Long reads
There’s more machinery than you think involved in running an Antarctic research station – and keeping the vehicles moving are a team of hardy and inventive engineers.Ben Norrish (Head of Vehicle Engineering) and Andy Warner (Vehicles Engineering Manager) explain why the team are ready for a workshop upgrade.
Nestled on the rocky shore of Adelaide Island, on the western side of the mountainous Antarctic Peninsula, a cluster of green and yellow buildings look out across the bay. This is Rothera Research Station – the largest of the UK’s polar research sites.With a rich history spanning the last 50 years, Rothera Research Station has enabled the UK to remain at the forefront of climate, biodiversity and ocean research in the Polar Regions. Staffed year-round, the station houses state-of-the art laboratories, diving and boating facilities, and is a vibrant focal point for marine and terrestrial biology, geology, glaciology, meteorology and upper atmospherics research. Just as importantly, Rothera is a hub for accessing the deep field for science – home to aircraft, the continent-roving tractor train traverse, and a fleet of vehicles that support operations on station and in the field.
In an environment as remote as Antarctica, every improvement to infrastructure and working conditions matters – and a big, blue building has recently joined the icy skyline. Intended to replace a number of older buildings, the newly constructed Discovery Building is now home to a purpose-built vehicles workshop.
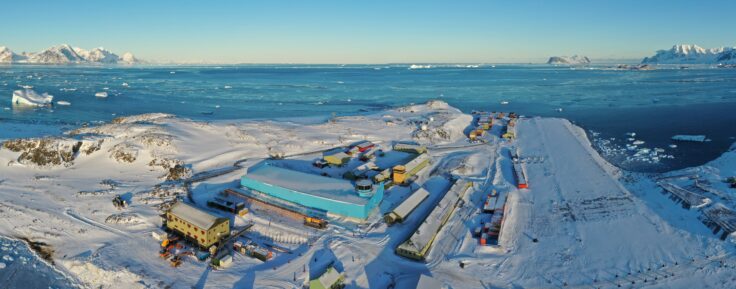
The new workshop has been designed to meet the demands of the station – which, crucially, have grown over the years. “Our current set-up is the same as when the garage was first built in 1977,” says Vehicles Engineering Manager, Andy Warner. “Our fleet of vehicles has grown a lot since then!”
The vehicles team are responsible for providing a high-quality fleet to support research and logistics in Antarctica. They oversee snow clearing at Rothera, essential for the continued safe and efficient management of air operations that underpin the BAS Science programme. The station has a high snowfall during the late winter, so two large attachment snow blowers are used to clear the runway and other important areas around station so that the season’s work can get underway.
The team also provide snowmobiles and tractor trains for deep field work, which transport science teams and their equipment across the vast remote areas UK scientists explore in the region.
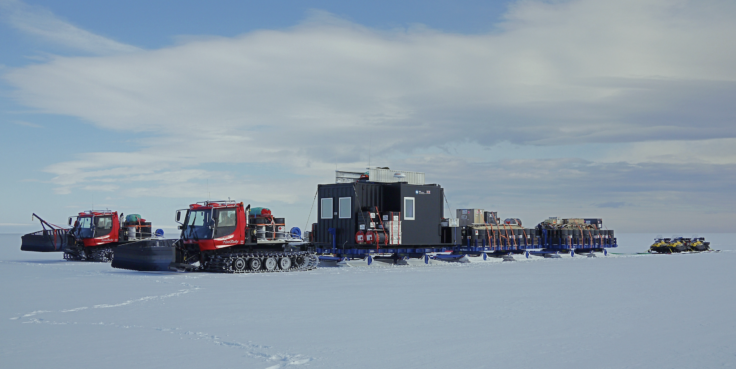
Ben Norrish, Head of Vehicle Engineering, explains why the team are so excited: :
“The existing workshop is no longer fit for purpose because of the size, weight and type of vehicles we’re working with now. There are at least three or four items of plant machinery we can’t physically get into the old building – two Volvo L180H wheeled loaders fitted with large snowblowers, and a trailer mounted 20-foot ISO container handler. So we’ve outgrown it.
The new facility allows us to get those vehicles under cover, which means we can carry out maintenance in a proper workshop environment. It’ll be clean, warm and dry – not just for the vehicles, but for our engineering technicians too – and the team are incredibly excited to move into our new home.”
The new space offers a more modern layout, improved lighting and – importantly – shelter from the elements a much-needed upgrade. It will make day to day operations more manageable and efficient.
A change from working in the cold
This team of eight heavy plant mechanics and three operators have to contend with all the kinds of challenges that Antarctica can throw at them – juggling the repairs and servicing of over 135 items of plant and machinery, including 51 snowmobiles.
Perhaps the most obvious obstacle is the cold. In the current set-up, much of their work takes place outside, or in buildings that have endured decades of harsh conditions. Winter storms, snow accumulation and cold temperatures affect everything: from the tools used, to the speed at which tasks can be completed.
In this context, one of the big improvements of the new workshop is simply scale, and vehicles that were previously exposed to snow and wind can now be thawed and maintained inside. Being able to work indoors, especially during winter, is good for both people and machines, as Andy explains:
“When you bring a vehicle in from the outside during the winter or after a big snowstorm, it’s important to thaw it properly, otherwise the water or ice can cause electrical faults. The new building will have hot air tubes that act like a large hairdryer. We can move them over the vehicle and melt it out much more quickly than before.
Previously, if we wanted to change a tyre, we’d have to do that outside in the cold because there wasn’t enough space indoors. Now we’ll be able to do all those tasks inside, in the warm, and that’s going to be far more comfortable.”
The larger layout allows engineers to work on multiple vehicles side-by-side, rather than the slower, end-to-end method used up to now. At the moment, the team have had to move all the vehicles outside every time they have needed to remove one, once work on it has been completed.
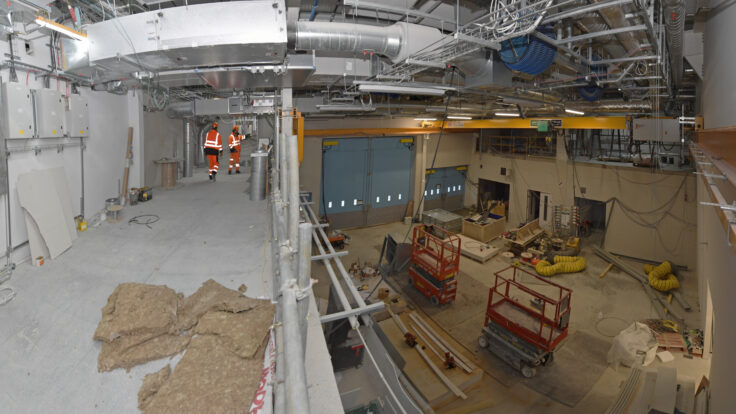
A key feature of the new workshop is the 5m x 5m blue door, inspired by the design used at Halley Research Station. By drawing on proven designs, the door brings an extra layer of reliability to Rothera’s new workshop. Built specifically for the Antarctic climate, the door opens outward to maximise interior space with an electrical actuator system, which uses an electric motor and unfolding arms to create the force needed so the doors open and close smoothly in freezing conditions. Heat traced concrete also provides an external surface clear of ice that allows internal-based vehicles to work effectively outside, moving the cargo loaded onto the concrete into the building.
“As contractors working in this environment, we know how challenging the snow and ice can be,” agreed Robert Kerr, Senior Agent at BAM. “We see this as a practical step towards greater operational resilience, especially at the start of the season when reliable access is essential.”
The move into the Discovery Building workshop is more than just a physical relocation. It represents a significant improvement in how the team will be able to operate.
“We’ve got much more flexibility in the new workshop,” Ben continues. “We now have a 3.5-tonne overhead gantry, so we can lift heavy items – engines, gearboxes, transmissions, tyres – and move them to any corner of the workshop. That’s something we never had before, and it’ll significantly reduce the amount of manual handling we do.”
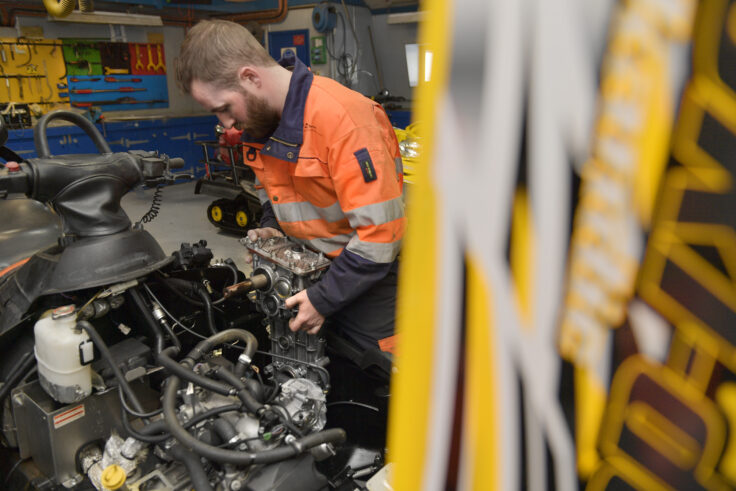
Along with extra space and new mezzanine structure, the workshop includes designated areas for different tasks, including separate dirty and clean zones. There’s a welding bay, a vehicle pit for low-slung vehicles, a fabrication space, and a machine room for engine and gearbox rebuilding.
“Parts and items are currently cramped on shelves in a one small room,” Andy continues. “Moving into a much larger store will allow us to lay everything out properly and work more efficiently. All of our stock will be accessible via the new mezzanine, and that means we can organise things in a way that works best for us.”
“The new layout also gives us a much better way to manage our inventory,” agrees Ben. “At the moment it is double stacked and hard to access. Now we’ll be able to process and store our goods properly and find what we need quickly when vehicles come in for servicing.”
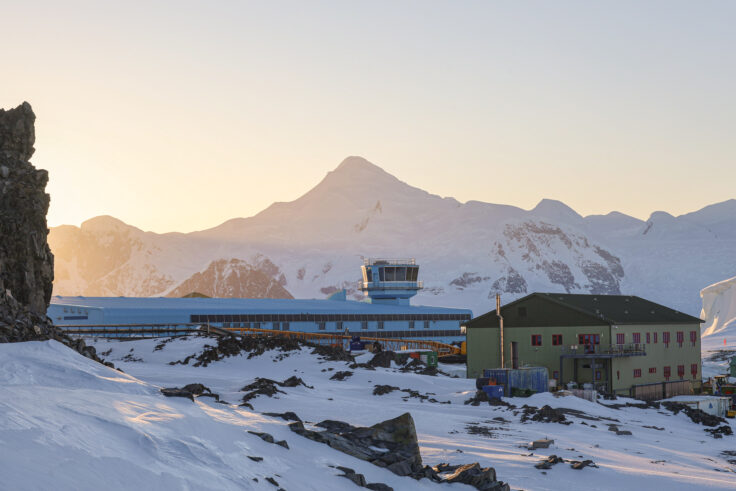
The true definition of a team
A modern workshop isn’t just about equipment and floor plans – it’s also a shared space where the engineering team spend much of their time. The people who live at Rothera Research Station form a close-knit group. Working and living together, this is a setting that demands cooperation and adaptability.
Reflecting on what it takes to keep the show on the road, Ben explains:
“In Antarctica, you can’t just ring up a parts dealer for an overnight delivery. You need foresight and imagination to keep things moving. If we have the right people on the ground, the issues, worries and problems tend to disappear. The team here are easy-going, supportive and always focused on finding solutions. That’s exactly what you need in this job.”
Teamwork and shared problem-solving are key to making progress in this remote setting. “You feel like part of a family down here,” he adds. “And that sense of belonging helps you through the difficult times. Everyone has moments when things are tough, and the team is always there to support each other.”
Andy also highlights how the close connections at Rothera help maintain morale:
“Because you’re so close to people from other roles, living and working together, you meet interesting people every day. You might find yourself chatting to an ocean scientist, a pilot, or an electrician. That variety keeps things fresh and makes each day different.”
Social events like Folk Night (a regular highlight at the station) play are part of the way that the team build their sense of community. “It’s a great way to lift spirits,” says Andy. “Folk Night usually marks the end of the field season, and is almost like a variety show. Whether it’s singing, dancing, comedy, or someone just having a go at something new, it brings everyone together.”
As the team prepares to move fully into the new workshop, there’s a shared sense of optimism.
“Everyone is looking forward to getting in there,” Ben says. “There’s a lot to do, and the transition won’t happen overnight. We still need to maintain the fleet while everything is moving, so it’s going to be a big effort. But it’ll be worth it.”
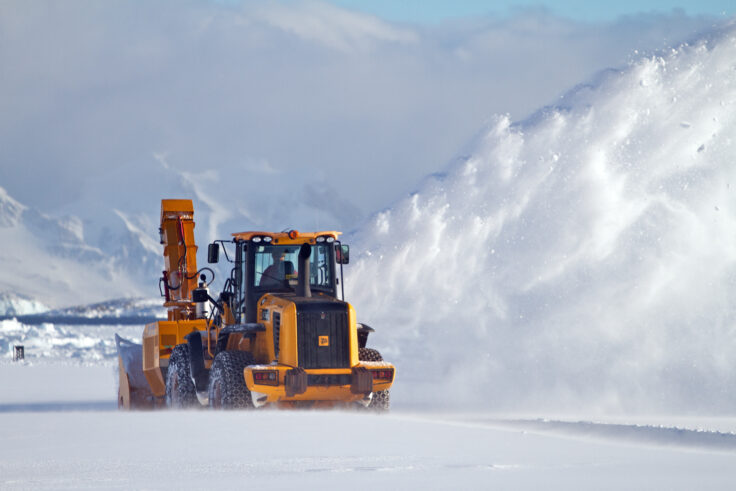
The new facility is more than just an upgrade, it’s an investment in the people and processes that keep science going in Antarctica.
“It’ll help everyone at BAS who supports science at Rothera,” Ben reflects. “We often need to adapt equipment or respond quickly to issues, and this space gives us the tools to do that.”
“Every time I step off the plane or the boat, I try to take a moment to look around and remember where I am. This is the gateway to Antarctica. It’s always a bit of a reset. And now, this is the next chapter for our team and we’re ready to get started.”
About the Antarctic Infrastructure Modernisation Programme
The Antarctic Infrastructure Modernisation Programme (AIMP) is part of the UK Government’s long-term investment in the Polar Regions. The programme is delivered in partnership with construction partners BAM UK & Ireland, Ramboll, Sweco and Hugh Broughton Architects.